Wie Sie die Produktionseffizienz Ihrer Verpackungslinie mit OEE verbessern können
Einer der besten Schlüsselindikatoren zur Bewertung und Verbesserung der Effizienz der Anlagen in einer automatischen Verpackungslinie ist die OEE (Gesamtanlageneffektivität). Sie ist ein entscheidender KPI zur Messung der Produktivität aller Prozesse und Produktionssysteme eines Unternehmens und ein Muss für die automatisierte Endlinie. OEE ist eine Kennzahl, die eng mit der Unternehmensphilosophie der kontinuierlichen Verbesserung, der Lean-Methodik und der Industrie 4.0 verbunden ist.
Im heutigen Artikel werden wir die OEE aus dem Blickwinkel einer Verpackungslinie analysieren und die wichtigsten Faktoren und Richtlinien zur Verbesserung der Effizienz an der Endlinie betrachten.
Was ist OEE und wie wirkt sie sich auf meine Verpackungslinie aus?
OEE misst die Effizienz von Produktionsanlagen, indem verschiedene Leistungsparameter der Maschinen berechnet werden. Die Analyse dieses Indikators ermöglicht es den Unternehmen, ihre Schwachstellen in Bezug auf Produktivitätsverluste, Engpässe, unnötige Stillstände und sogar Mängel und Ausschuss zu ermitteln. Infolgedessen ist es für das Unternehmen einfacher, Verbesserungen umzusetzen, die Qualität der Produktion zu erhöhen und letztlich die Kundenzufriedenheit zu steigern, indem u. a. die Lieferzeiten für Waren verkürzt und fehlerhafte Einheiten eliminiert werden.
In einer Endverpackungslinie ist es wichtig, die OEE zu verstehen, um die Produktivität und die Geschwindigkeit der Linie zu erhöhen, Verpackungsfehler zu reduzieren, die Qualität der Verpackung zu verbessern usw.
Wie wird die OEE berechnet und was ist der optimale Indikator?
Bei der OEE werden drei Variablen berücksichtigt: Verfügbarkeit, Leistung und Qualität, die multipliziert werden, um den endgültigen Leistungskoeffizienten zu erhalten. Schauen wir uns an, wie sie in einer Verpackungslinie angewendet werden:
Verfügbarkeitsindikator:
Die Anlagenverfügbarkeit wird berechnet, indem die produktive Zeit (Zeit, in der die Anlage ohne Unterbrechungen arbeitet) durch die geplante Produktionszeit (oder ihre theoretische Verfügbarkeit) geteilt wird. Geplante Abschaltungen (geplante Feiertage, Abschaltungen wegen geplanter Wartungsarbeiten usw.) werden in diesem Punkt nicht berücksichtigt.
In einer Verpackungslinie können der Wechsel von Verbrauchsmaterialien (Folie, Umreifungsrollen usw.), Stillstandzeiten aufgrund von Änderungen der Rotationsschichten, Stillstandzeiten aufgrund von Pannen oder Ausfällen, Änderungen des Palettenformats, die zu Prozesspausen führen, usw. als unproduktive Zeit gezählt werden.
Die Folge ist ein Verlust an Maschinenverfügbarkeit durch Produktionsstillstand.
Leistungsindikator
Dieser Leistungsindikator wird ermittelt, indem die tatsächliche Produktionszeit (die sich aus der Berechnung der Verfügbarkeitsquote ergibt) durch die theoretische Produktion geteilt wird, die entsprechend der maximalen Leistung der Maschinen oder dem Prozess der Linie selbst definiert ist.
Bei einer Verpackungslinie beispielsweise wird die tatsächliche Produktionszeit der Linie durch die maximale Leistung der verschiedenen Verpackungssysteme geteilt.
Die Zahl, die sich aus diesem Indikator ergibt, ist der Leistungsverlust oder die überschüssige Produktionszeit der Verpackung.
Qualitätsindikator:
Der Parameter Qualität schließlich ist das Ergebnis der Division der tatsächlichen Produktionszeit (Beseitigung von Stopps, fehlerhaften Teilen usw.) durch die theoretische Produktionszeit bei maximaler Leistung der Maschine (erwartete tatsächliche Produktion). Das heißt, in einer Verpackungslinie wird die Produktion von korrekt verpackten Paletten (ohne Fehler) durch die allgemeine Produktionszeit aller Paletten, die die Linie verlassen haben, geteilt.
Dadurch geht die Zeit verloren, die für die Produktion fehlerhafter oder zurückgewiesener Einheiten aufgewendet wird.
Endgültiger OEE-Indikator
Das Ergebnis der gesamten Maschineneffektivität, einschließlich der Verluste, ergibt sich aus der Multiplikation der drei Indikatoren für Verfügbarkeit, Leistung und Qualität. Der endgültige Indikator wird als Prozentsatz ausgedrückt, mit einem Wert zwischen 0 und 100 %, wobei 100 % natürlich das optimale Produktionsergebnis darstellt, bei dem nur gute Teile mit maximaler Geschwindigkeit und ohne Ausfallzeiten produziert werden.
Ein Mindest-OEE-Indikator liegt bei über 70 %, da ein Wert darunter bedeutet, dass das Unternehmen viele Ausschüsse, fehlerhafte Waren, Ausfälle und ständige Stillstandszeiten in seinen Produktionslinien hat, was zu großen Umsatzeinbußen führt.Über 85 % OEE ist der Prozentsatz, der erforderlich ist, um „World Class Manufacturing Excellence“ zu erreichen, ein wichtiger Meilenstein für viele Unternehmen.
Nachstehend finden Sie eine Tabelle zur Berechnung der OEE entsprechend der zeitlichen Aufteilung Ihrer Verpackungsanlagen:
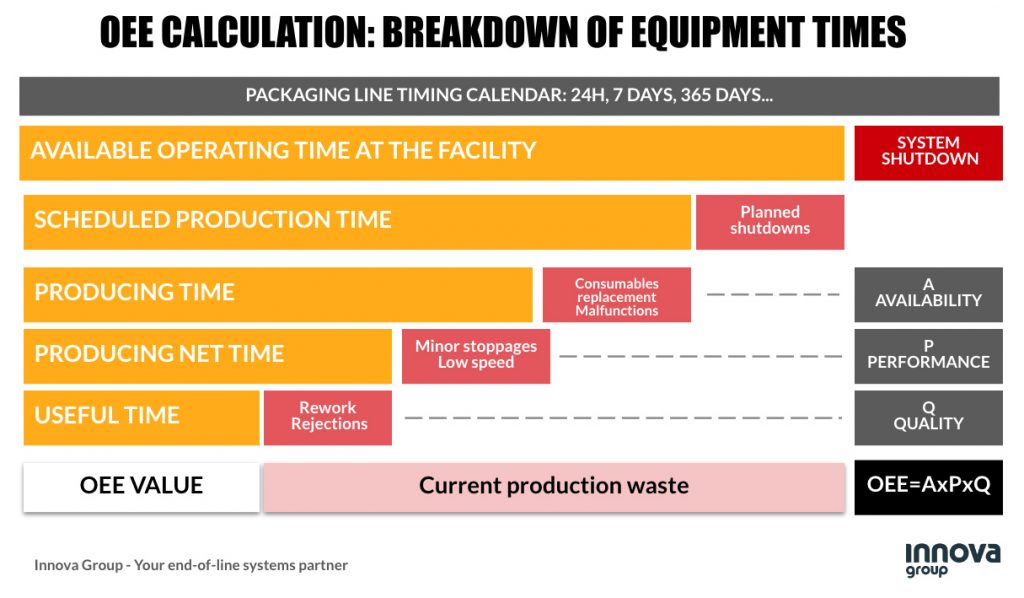
Wie kann ich die Effizienz meiner Verpackungslinie und die OEE verbessern?
Es gibt viele Aspekte, die sich auf die Verbesserung der Linieneffizienz auswirken, und wenn die OEE noch viel Raum für Wachstum hat, gibt es einige Korrekturmaßnahmen, die kurz- bis mittelfristig zu einem recht schnellen Erfolg führen können.
Ausgehend von unserer Erfahrung als Hersteller von Endliniensystemen und unserer Erfahrung mit der Lean-Fertigungs-Methodik erläutern wir einige wichtige Maßnahmen und Richtlinien zur Verbesserung der Effizienz:
- Erneuerung veralteter Anlagen und stärkere Automatisierung: Eine der offensichtlichsten Maßnahmen ist die Erneuerung der Palettenverpackungssysteme, die viele Ausfallzeiten und ständige Pannen verursachen. Auch bei nicht automatisierten Prozessen ist es ratsam, in automatische Verpackungssysteme zu investieren, da sie viele Vorteile bieten und sich im Vergleich zu den Verlusten und der Langsamkeit manueller Prozesse schnell amortisieren.
- Vorbeugende Wartung: Die Wartung ist nicht nur wichtig, um die Ausfallzeiten von Verpackungsanlagen zu reduzieren, sondern auch, um deren Leistung zu verbessern. Wesentlich ist dabei, dass das Wartungsprogramm so geplant wird, dass es nicht auch einen größeren Anlagenstillstand betrifft und dass es während bereits geplanter Stillstandszeiten (z.B. saisonal, Ferien) durchgeführt wird.
- Direkter Service vom Hersteller: Es wird empfohlen, dass der Gerätehersteller (OEM) auch Ihr Lieferant für Wartungsdienste, technische Unterstützung usw. ist. Nicht nur wegen der Schnelligkeit und der Verringerung der Ausfallzeiten, sondern auch wegen seiner umfangreichen Erfahrung in der Branche, um eine bessere Verpackung Ihrer Waren zu erhalten (besserer Schutz, sicherer für den Transport usw).
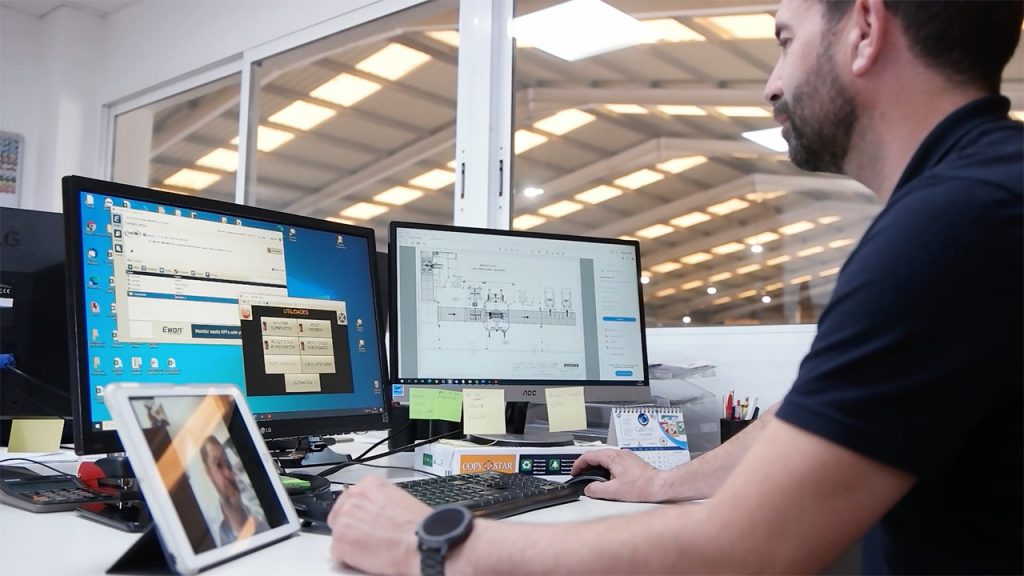
- Sofortige Ersatzteile: Ob durch einen Hersteller, der den Service anbietet, oder durch ein eigenes Ersatzteillager, es ist ein Schlüsselelement zur Verringerung der Ausfallzeiten durch den Austausch von Teilen.
- Qualitätskontrolle der Verpackungen: Wenn das Unternehmen nicht darüber verfügt, ist dies ein unmittelbarer Verbesserungspunkt, der den OEE-Indikator erhöhen wird. Es geht um die Umsetzung von Qualitätskontrollplänen im Verpackungsprozess, um sicherzustellen, dass die Waren die für den Transport und/oder vom Kunden geforderten Qualitätsstandards erfüllen. Sobald Fehler und Ausschuss entdeckt werden, können sie mit Hilfe des Herstellers und seines Wartungsdienstes behoben werden.
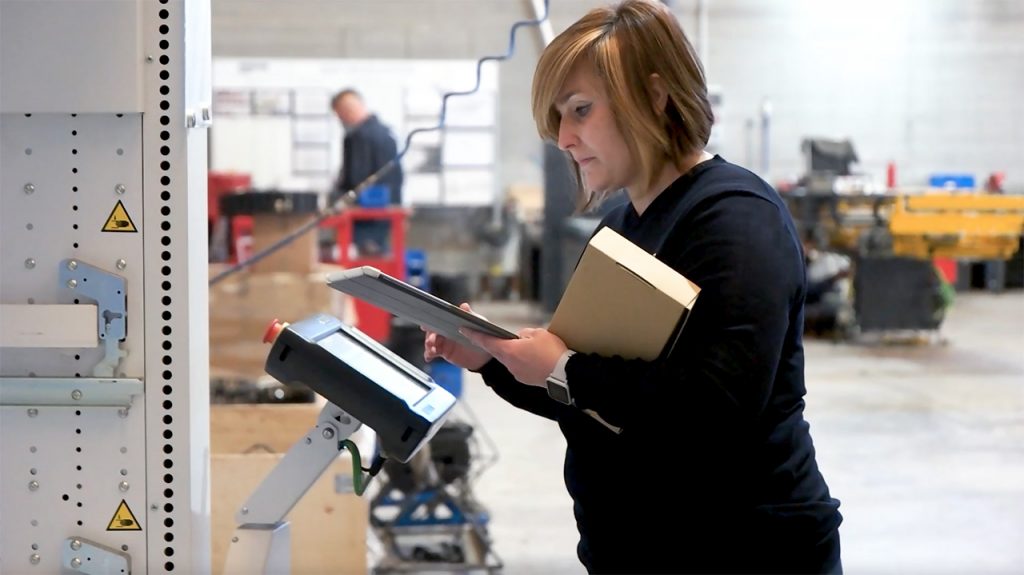
- Kontinuierlicher Schulungsplan: Außerdem ist es wichtig, dass das technische Personal der Linie eine spezielle Schulung für den ordnungsgemäßen Betrieb, den Austausch von Verbrauchsmaterialien und die allgemeine Fehlersuche erhält. Es ist wichtig, dass das Personal nicht nur bei der Inbetriebnahme der Anlage geschult wird, sondern in regelmäßigen Abständen, wenn sich das Personal ändert oder die Maschinen aufgerüstet werden.
- Schnellerer Wechsel der Verbrauchsmaterialien: Ein weiterer Aspekt der automatischen Systeme ist, dass sie den Wechsel der Folien- oder Umreifungsrollen erleichtern, um die Ausfallzeiten so weit wie möglich zu reduzieren. Bei Innova bieten wir zum Beispiel Systeme mit mehreren Rollen an, wie die Wickelmaschine mit doppeltem Folienwagen oder das Stretch Hood-System mit 3 Folienrollen, um eine größere Kontinuität in der Linie zu gewährleisten, ohne dass es zu Ausfallzeiten für den Folienwechsel kommt. Durch die Wahl eines Wickelsystems anstelle eines anderen werden diese Stopps ebenfalls reduziert: Während ein herkömmlicher Paletten-Stretch-Wickler 150-200 Paletten ohne Folienwechsel wickelt, können mit dem Stretch Hood-System rund 1.000 Paletten ohne Rollenwechsel gewickelt werden, da weniger Kunststoff pro Palette und Rollen mit einer größeren Folienmenge verwendet werden.
- Mit Volldampf voraus! Lassen Sie die Maschine laufen! Wie bei den alten Dampflokomotiven ist es ratsam, dass die Maschinen nicht zu viele Stopps einlegen, vor allem nicht über längere Zeiträume hinweg. Eine Maschine, die sich in ständiger Produktion befindet, wird weniger Probleme haben, da sie regelmäßiger gewartet wird (Schmieren und Reinigen von Teilen) und letztendlich eine bessere Leistung erbringt.
Zusammenfassend lässt sich sagen, dass es viele Parameter gibt, die zur Verbesserung der Effizienz einer Verpackungslinie eingesetzt werden können, die auch für jede andere Produktionsanlage gelten. Es ist wichtig, diesen Koeffizienten der kontinuierlichen Verbesserung zu berücksichtigen, um die „unsichtbaren“ Verluste (Zeitverluste und Schäden an Waren) unter Kontrolle zu halten, die am Ende des Jahres zu einem Problem für die Produktion und sogar für den Umsatz des Unternehmens werden können.
Als auf automatische Verpackungslinien spezialisierter Hersteller kann die Innova-Gruppe Sie bei der Optimierung Ihrer Verpackungsanlagen und der Reduzierung von Fehlern und Ausfallzeiten beraten. Zögern Sie nicht, unser technisches Verkaufsteam für eine unverbindliche Beratung zu kontaktieren.
Interessieren Sie sich für unsere Fachartikel zum Thema Verpackung und Logistik? Abonnieren Sie unseren monatlichen technischen Newsletter!